How Carbon Fiber Automotive Parts are Manufactured Using an Autoclave
The production of carbon fiber automotive parts using an autoclave is a sophisticated process that ensures high strength and lightweight characteristics. Below are the detailed steps involved in this manufacturing method:
1. Preparing the Carbon Fiber Layup
The process begins with the preparation of the carbon fiber layup. Carbon fiber fabric or prepreg (pre-impregnated with resin) is cut into specific shapes and sizes according to the part design. The layers of carbon fiber are carefully arranged in a mold to achieve the desired thickness and structural properties. This step is crucial as it determines the strength and performance of the final part.

2. Loading into the Mold
Once the carbon fiber layup is prepared, it is placed into a mold that defines the shape of the automotive part. The mold is designed to withstand the high pressures and temperatures within the autoclave. The carbon fiber layers are carefully positioned within the mold to ensure proper alignment and to avoid any defects or air pockets.
3. Placing in the Autoclave
The mold containing the carbon fiber layup is then placed into the autoclave. An autoclave is a high-pressure vessel that can apply both heat and pressure simultaneously. This step is critical for the curing process of the carbon fiber.
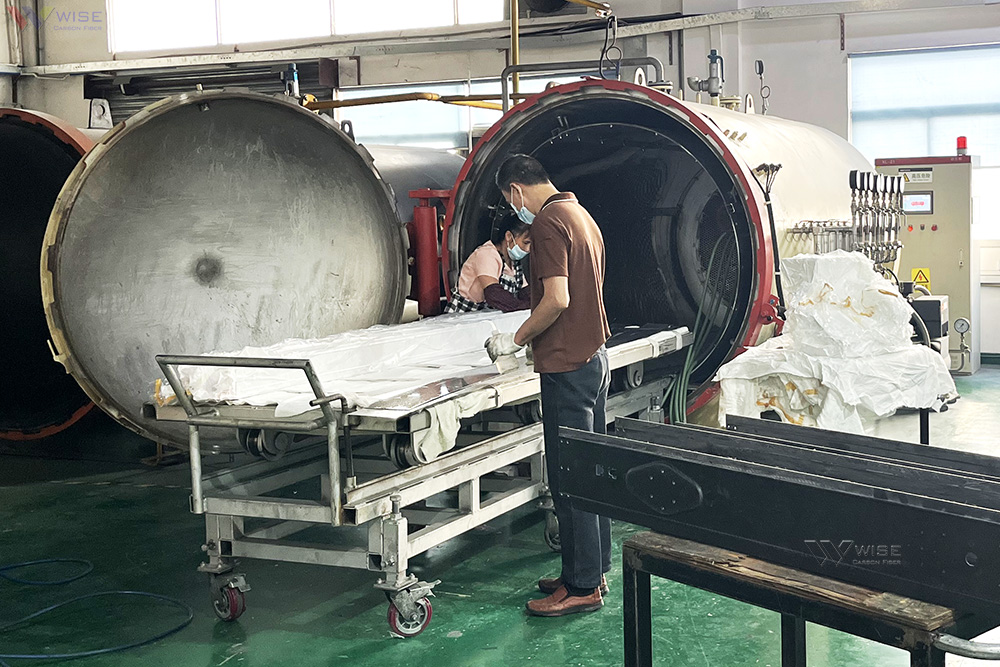
4. Applying Heat and Pressure
Inside the autoclave, the temperature is gradually increased to the required level, usually between 120°C to 180°C (248°F to 356°F), depending on the resin system used. The pressure is also increased, typically ranging from 50 psi to 100 psi. The combination of heat and pressure allows the resin to flow and fully impregnate the carbon fiber, ensuring a strong bond between the fibers.
5. Curing Process
The curing process involves maintaining the temperature and pressure for a specific duration, usually several hours. During this time, the resin undergoes a chemical reaction that causes it to harden and cure, forming a solid composite material. The controlled environment within the autoclave ensures that the curing process is uniform, resulting in a high-quality part with optimal mechanical properties.
6. Cooling and Demolding
After the curing process is complete, the autoclave is gradually cooled to room temperature. The mold is then removed from the autoclave, and the cured carbon fiber part is carefully taken out of the mold. This step requires precision to avoid damaging the part.
7. Finishing and Inspection
The final step involves finishing and inspection. The carbon fiber part is trimmed to remove any excess material and achieve the precise dimensions required. It is then inspected for any defects or inconsistencies. Non-destructive testing methods, such as ultrasonic inspection, are often used to ensure the integrity of the part.

Conclusion
The use of an autoclave in the production of carbon fiber automotive parts ensures the highest quality and performance. The process involves meticulous preparation, precise application of heat and pressure, and thorough inspection, resulting in parts that are strong, lightweight, and ideal for high-performance automotive applications.
WISE have 12 years carbon fiber molding experience, has a rich technical reserve, you can trust us to handle your project and feel free to customize your product.
1. Preparing the Carbon Fiber Layup
The process begins with the preparation of the carbon fiber layup. Carbon fiber fabric or prepreg (pre-impregnated with resin) is cut into specific shapes and sizes according to the part design. The layers of carbon fiber are carefully arranged in a mold to achieve the desired thickness and structural properties. This step is crucial as it determines the strength and performance of the final part.

2. Loading into the Mold
Once the carbon fiber layup is prepared, it is placed into a mold that defines the shape of the automotive part. The mold is designed to withstand the high pressures and temperatures within the autoclave. The carbon fiber layers are carefully positioned within the mold to ensure proper alignment and to avoid any defects or air pockets.
3. Placing in the Autoclave
The mold containing the carbon fiber layup is then placed into the autoclave. An autoclave is a high-pressure vessel that can apply both heat and pressure simultaneously. This step is critical for the curing process of the carbon fiber.
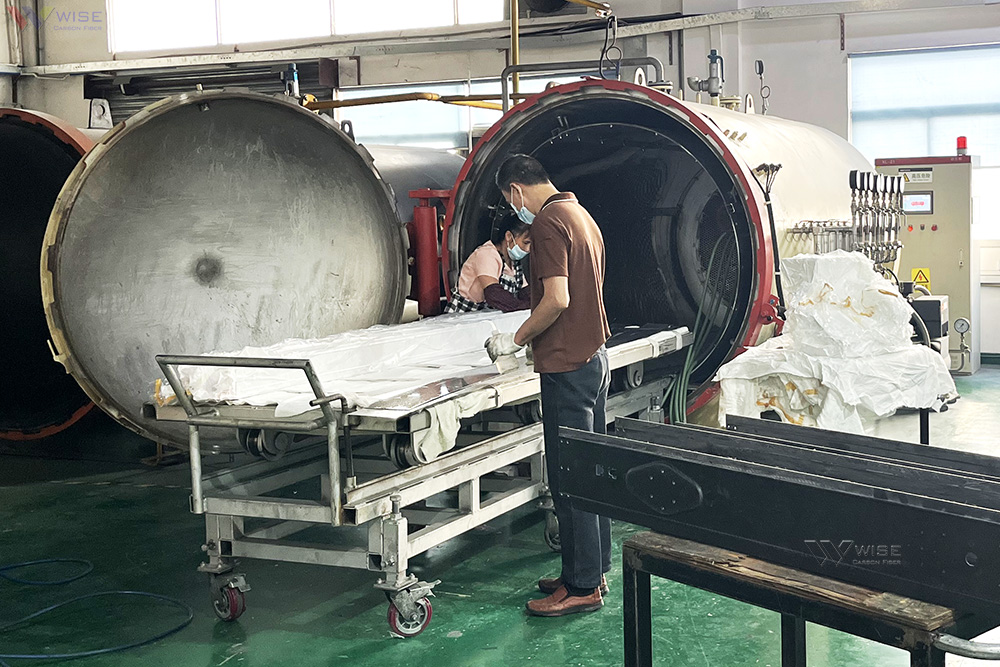
4. Applying Heat and Pressure
Inside the autoclave, the temperature is gradually increased to the required level, usually between 120°C to 180°C (248°F to 356°F), depending on the resin system used. The pressure is also increased, typically ranging from 50 psi to 100 psi. The combination of heat and pressure allows the resin to flow and fully impregnate the carbon fiber, ensuring a strong bond between the fibers.
5. Curing Process
The curing process involves maintaining the temperature and pressure for a specific duration, usually several hours. During this time, the resin undergoes a chemical reaction that causes it to harden and cure, forming a solid composite material. The controlled environment within the autoclave ensures that the curing process is uniform, resulting in a high-quality part with optimal mechanical properties.
6. Cooling and Demolding
After the curing process is complete, the autoclave is gradually cooled to room temperature. The mold is then removed from the autoclave, and the cured carbon fiber part is carefully taken out of the mold. This step requires precision to avoid damaging the part.
7. Finishing and Inspection
The final step involves finishing and inspection. The carbon fiber part is trimmed to remove any excess material and achieve the precise dimensions required. It is then inspected for any defects or inconsistencies. Non-destructive testing methods, such as ultrasonic inspection, are often used to ensure the integrity of the part.

Conclusion
The use of an autoclave in the production of carbon fiber automotive parts ensures the highest quality and performance. The process involves meticulous preparation, precise application of heat and pressure, and thorough inspection, resulting in parts that are strong, lightweight, and ideal for high-performance automotive applications.
WISE have 12 years carbon fiber molding experience, has a rich technical reserve, you can trust us to handle your project and feel free to customize your product.